交流异步电机软起动及其优化节能控制技术介绍
本文引用地址://m.amcfsurvey.com/article/159851.htm
(2)电压斜坡起动:输出电压由小到大斜坡线性上升,将传统的降压起动变有级为无级,主要用在重载起动。它的缺点是起动转矩小,且转矩特性呈抛物线型上升对起动不利,且起动时间长,对电机不利。改进的方法是采用双斜坡起动:输出电压先迅速升至U1,U1为电动机起动所需的最小转矩所对应的电压值,然后按设定的速率逐渐升压,直至达到额定电压。初始电压及电压上升率可根据负载特性调整。这种起动方式的特点是起动电流相对较大,但起动时间相对较短,适用于重载起动的电机。
(3)转矩控制起动:主要用在重载起动,它是按电动机的起动转矩线性上升的规律控制输出电压,它的优点是起动平滑、柔性好,对拖动系统有利,同时减少对电网的冲击,是最优的重载起动方式。它的缺点是起动时间较长。
(4)转矩加突跳控制起动:转矩加突跳控制起动与转矩控制起动一样也是用在重载起动的场合。所不同的是在起动的瞬间用突跳转矩,克服拖动系统的静转矩,然后转矩平滑上升,可缩短起动时间。但是,突跳会给电网发送尖脉冲,干扰其它负荷,使用时应特别注意。
(5)电压控制起动:电压控制起动是用在轻载起动的场合,在保证起动压降的前提下使电动机获得最大的起动转矩,尽可能地缩短起动时间,是最优的轻载软起动方式。各种软起动方式的相应起动曲线见图2。
停车方式有三种:一是自由停车,二是软停车,三是制动停车。软起动器带来的最大好处是软停车和制动停车,软停车消除了拖动系统的反惯性冲击,对于水泵就是“水锤”效应;制动停车则在一定场合代替了反接制动停车功能。
2.4软起动器与传统降压起动器的比较
软起动器与传统降压起动器的性能比较见表1。
2.5软起动器的适用场合
(1)生产设备精密,不允许起动冲击,否则会造成生产设备和产品不良后果的场合;
(2)电动机功率较大,若直接起动,要求主变压器 产品主要性能数字式软起动器磁控降压起动器自耦降压起动器
起动特性软特性:用户可以调整特性较硬:不能调整硬特性:不能调整
起动电流特性曲线
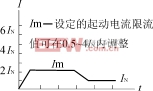
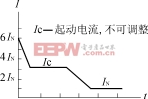
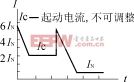
起始电压0~380V任意可调200V左右:用户不能调整250V左右:用户不能调整
起动冲击电流无1次,约为电机额定电流IN的6倍2次,约为电机额定电流IN的7倍
起动电流(0.5~4)IN,用户可视负载轻重调整(2~3)IN以上,不能调整(3~5)IN以上,不能调整
电机转矩特性没有冲击转矩,力矩匀速平滑上升1次冲击转矩后,力矩匀速平滑上升力矩跳跃上升,有2次冲击转矩
负载适应能力强一般较差
能否频繁起动可以一般不能一般不能
起动方式限流软起动或电压斜坡起动任选区域恒流软起动分段式恒压起动
执行元件电力电子器件磁饱和电抗器(磁放大器)自耦变压器
控制元件和控制方式16位高性能单片计算机模糊控制继电器及普通电子元件继电电子控制继电器继电控制
整机重量/体积轻/小较重/较大重/大
外接电缆数量6根(3进、3出)6根或9根(130kW以上为:3进、6出)6根(3进、3出)
表1软起动器与传统降压起动器的比较
容量加大的场合;
(3)对电网电压波动要求严格,对压降要求≤
10%UN的供电系统;
(4)对起动转矩要求不高,可进行空载或轻载起
动的设备。
严格地讲,起动转矩应当小于额定转矩50%的拖动系统,才适合使用软起动器解决起动冲击问题。对于需重载或满载起动的设备,若采用软起动器起动,不但达不到减小起动电流的目的,反而会要求增加软起动器晶闸管的容量,增加成本;若操作不当,还有可能烧毁晶闸管。此时只能采用变频软起动。因为软起动器调压不调频,转差功率始终存在,难免产生过大的起动电流;而变频器采用调频调压方式,可实现无过流软起动,且可提供1.2~2倍额定转矩的起动转矩,特别适用于重载起动的设备。但是变频器的价格要比软起动器的价格高得多了。
对于满载或重载运行的电动机,降低其端电压将会造成严重后果,随着端电压的降低,电动机的磁通和电动势随之减小,铁耗无疑将下降。但与此同时,随电压平方变化的电动机转矩也迅速下降而小于负载转矩,电动机只能依靠增大转差率,提高电磁转矩以达到与负载转矩相平衡的状态。转差率的增大,引起转子电流增大,同时引起定子和转子电压间的相角增大,导致定子电流增大,从而使定子和转子铜耗增加值大大超过铁耗的下降值,这时电动机绕组温升将会增高,效率将会下降,甚至发生电动机烧毁事故。因而,一般规程都规定了电动机正常运行时电压变化范围不得超过额定电压的95%~110%。
然而对于轻载运行的电动机,情况就截然不同,使供电电压适当降低,在经济上是有利的。这是因为在轻载运行时,电动机的实际转差率大大小于额定值,转子电流并不大,在降压运行时,转子电流增加的数值有限。而另一方面,却由于电压的降低,使空载电流和铁损大幅减少。在这种情况下,电动机的总损耗就可降低,定子温升,运行效率和功率因数同时得到改善。由此可见,电动机的运行经济性与电动机负载率同运行电压是否合理匹配关系极大。理论分析表明电动机的力能指标(运行效率与功率因数)与其端电压之间存在如下的数量关系[2]:
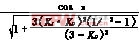
cosφ=(1)

η=(2)
式中:SN和S为电动机额定工况和降压运行的转差率;cosφN和cosφ为电动机额定工况和降压运行的功率因数;
ηN和η为电动机额定工况和降压运行的效率;
KU为电动机的调压系数,KU=U/UN(UN和U为电动机额定电压和降压运行时的实际电压);
KI为电动机的空载电流系数,KI=IO/IN(IN和
IO为电动机的额定电流和空载电流)。
从式(2)不难看出:并不是所有的降压行为都能达到节电的目的,只有当电压降低程度大于转差率及功率因数上升程度时,才能使运行效率提高。实际上,电动机效率随电压降低而变化的关系呈马鞍形曲线,对应于每一个输出功率(或负载系数),必然存在一个最佳调压系数KUm,当KU=KUm时,电动机的损耗最低,效率最高。KUm称为电动机的最佳电压调节系数。不同负载下最佳电压调节系数KUm可按电动机的负载系数β由下式确定[1]:

KUm=(3)
式中:ΣPN为电动机额定负载时的有功损耗(kW);
PO为电动机的空载损耗(kW);
K为计算系数,K=(PO-Pfw)/ΣPN〔Pfw为电
动机的机械损耗(kW)〕;
β为电动机的负载系数,β=(P2/PN)·100%
(P2为电动机的输出功率,PN为电动机的
额定功率)。
文献[1]给出了轻载电动机采用降压节电措施后,节约电能的计算公式为:
节约的有功功率ΔP为:
ΔP=(ΣPN-PO)β2(1-1/KU2)+ΣPN(1-KU2)(4)
节约的无功功率ΔQ为:

ΔQ=(QN-QO)β2(1-)+QO(1-KU2)(5)
式中:QN为电动机带额定负载时的无功功率(kvar);
QO为电动机的空载无功功率(kvar)。
节约的电能ΔAC为:
ΔAC=Tec(ΔP+KQΔQ)(6)
式中:KQ为无功经济当量,当电动机直连电机母线
KQ=0.02~0.04,二次变压取KQ=0.05~
0.07,三次变压取KQ=0.08~0.10;
Tec为电动机年运行时间(h)。
3.2优化节电的控制依据
(1)功率因数(cosφ)控制法
最早出现的异步电机优化节电器为Nolacosφ功率因数控制器,其原理是通过检测电动机运行中的cosφ值,与预先设定的基准值比较,当实际值低于设定值时,说明电动机为轻载,通过降低电动机的端电压来提高cosφ,直到实际的cosφ测量值达到设定值为止,实现了节电;cosφ数值高表明是重载,则升高电机端电压,以保证轴上的输出功率。这是一种间接节电法:控制对象是电动机的功率因数,而目的是节电。由于交流异步电机的最佳功率因数在全工作范围内呈曲线变化;不同制造厂生产的同一规格的异步电机的功率因数呈一定的离散性;同一台电机在其寿命期不同阶段,在同一工况下的功率因数也呈现一定的离散性,这就给设计和调整带来一定的困难。故这种方法不能达到最佳节电效果,并且理论与实践都已证明,过高的功率因数值对于异步电机来说,并不节电。
(2)最小输入功率法
交流异步电机工作时,从电网输入的电功率P1,一部分转换成电机轴上的机械功率P2输出,另一部分则是自身的损耗PS,包括铁耗与铜耗两部分。其中铁耗与输入电压的平方成正比,而铜耗则与其电流的平方成正比,只有在铜耗等于铁耗时,电机的效率最高,损耗PS最小。最小输入功率法的原理就是在电机工作的任一负载点上,在保证轴上机械功率输出的前提下,通过降低电机的端电压而减小电机自身的损耗,从而达到节能的目的。虽然降压可以降低铁耗,而当电压降到一定程度之后,若继续下降,则电流又要增加,因而又增加了铜耗。通过微机自动寻优,让铁耗和铜耗都维持在最低的水平,也即电压与电流的乘积——输入的电功率达到最小值,实现最优节电目的。
评论